Pace Industries Announces Doug Albert, as Chief Executive Officer
Pace Industries, LLC (“Pace” or the “Company”), North America’s leading full-service aluminum, zinc and magnesium die casting manufacturer, today announced that Doug Albert has been appointed as Chief Executive Officer.
Mr. Albert brings more than 20 years of leadership experience in the industrial sector, having served in a range of general management, commercial, manufacturing, financial, and operational roles. From 2014 until its sale in 2022, Mr. Albert was the President and Chief Executive Officer of Resco Products, Inc., a leading North American manufacturer of refractory products serving steel and industrial end markets. At Resco Products, he oversaw key strategic initiatives that drove growth and improvements in commercial, operating, and financial performance.
“Doug is a seasoned leader bringing a deep understanding of our customers, markets, and industry,” said Jeffrey P. Pritchett, Executive Chairman of Pace. “His knowledge, combined with an impressive commercial and operational background, makes him a great fit for Pace. Alongside our talented team, Doug will help Pace become an even stronger partner to our customers and expand in our core markets. We’re thrilled to have him at the helm in this next chapter of growth for Pace.”
Prior to Resco Products, Mr. Albert held leadership positions at Environmental Filtration Technologies and GE Fanuc Automation. Earlier in his career, he spent several years at global consulting firm Booz Allen where he supported a broad range of companies on manufacturing and supply chain management strategies. Mr. Albert earned a B.S. in Mechanical Engineering from the University of Rochester and received an MEM and MBA from Northwestern University’s McCormick School of Engineering and its J.L. Kellogg Graduate School of Management, respectively.
Mr. Albert added: “Pace has been a trusted partner for more than 50 years because of its unwavering commitment to quality and value. This is a dynamic time for the Company, and I’m excited to join the dedicated team. Together, we’ll strengthen our platform, accelerate our commercial strategy, and expand in strategic markets. I’m grateful to Pace’s Board and shareholders for their support and look forward to delivering best-in-class service and great value to customers.”
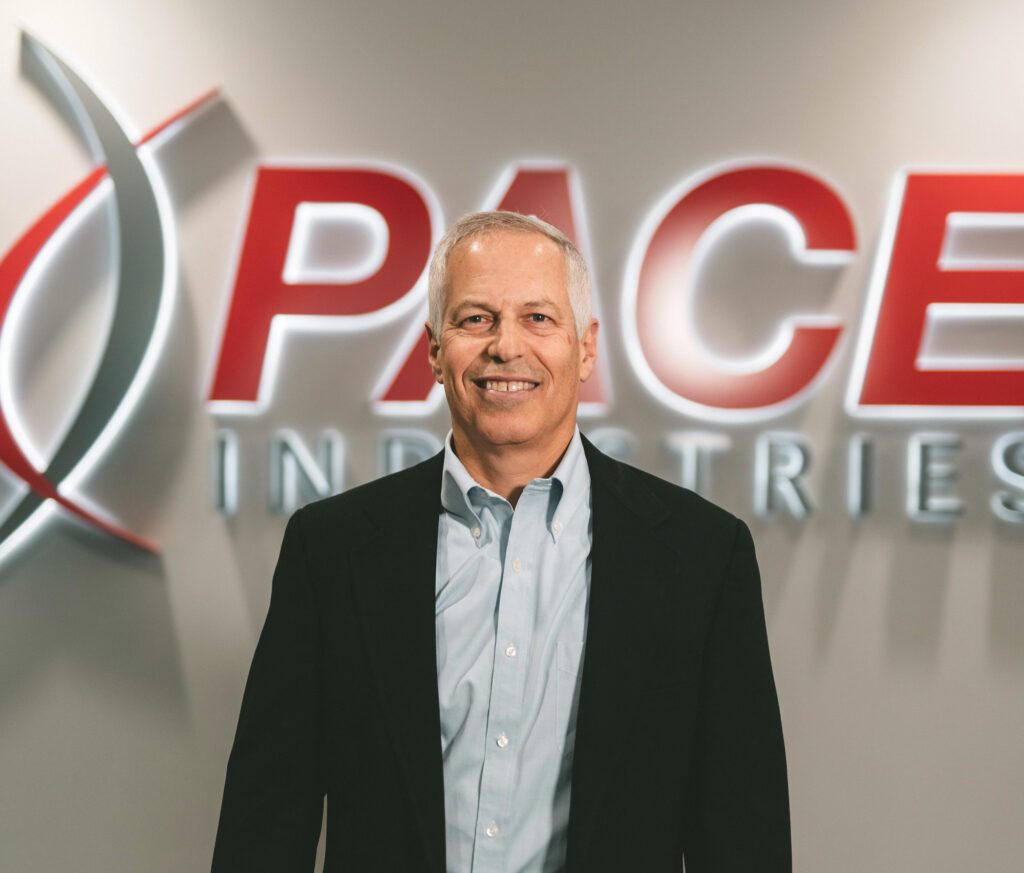