CAPABILITIES
ZINC DIE CASTING
Pace, a company specializing in zinc die casting, offers a variety of zinc die casting approaches that range from the ability to produce small, miniature zinc die castings to larger, conventional castings.
PACE INDUSTRIES
ZINC DIE CASTING
As a leading zinc die casting company, Pace offers offer an array of secondary and value-added services to provide completely finished and assembled products. Pace’s manufacturing facilities have Techmire machines for miniature zinc die castings, as well as conventional die casting machines ranging from 60 to 650 tons.
PACE INDUSTRIES
ZINC DIE CASTING
As a leading zinc die casting company, Pace offers offer an array of secondary and value-added services to provide completely finished and assembled products. Pace’s manufacturing facilities have Techmire machines for miniature zinc die castings, as well as conventional die casting machines ranging from 60 to 650 tons.
ADVANTAGES OF ZINC DIE CASTING

Good Strength and Hardness

Excellent Electrical Conductivity

Ability to Cold Form to Ease Joining

High Quality Finishing Characteristics

Outstanding Corrosion Resistance
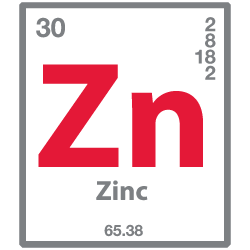

High Thermal Conductivity

Low Cost Raw Material

Full Recyclability

High Dimensional Accuracy and Stability

Outstanding Thin Wall Capability
ADVANTAGES OF ZINC DIE CASTING

Good Strength and Hardness

Excellent Electrical Conductivity

Ability to Cold Form to Ease Joining

High Quality Finishing Characteristics

Outstanding Corrosion Resistance
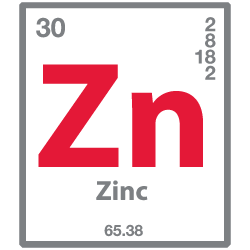

High Thermal Conductivity

Low Cost Raw Material

Full Recyclability

High Dimensional Accuracy and Stability

Outstanding Thin Wall Capability
ZINC
METAL OF CHOICE
Zinc offers a combination of characteristics that gives it a unique advantage in many die casting applications. These include a combination of strength, ductility, impact strength, finishing characteristics and tooling that has high resistance to catastrophic failure.
Zinc is the heaviest of the three alloy groups our die casting company offers, weighing approximately 2.5 times more than aluminum and 3.25 times more than magnesium. Further, zinc tools typically last between 400,000 and 700,000 shots depending on the design. With these factors and the finishing advantages of zinc, it’s easy to see why this is a metal of choice for many applications.
ZINC
METAL OF CHOICE
Zinc offers a combination of characteristics that gives it a unique advantage in many die casting applications. These include a combination of strength, ductility, impact strength, finishing characteristics and tooling that has high resistance to catastrophic failure.
Zinc is the heaviest of the three alloy groups our die casting company offers, weighing approximately 2.5 times more than aluminum and 3.25 times more than magnesium. Further, zinc tools typically last between 400,000 and 700,000 shots depending on the design. With these factors and the finishing advantages of zinc, it’s easy to see why this is a metal of choice for many applications.
ZINC ALLOYS
OFFERINGS
VIEW PROPERTIES
ZAMAK 2 (ASTM AC43A)
Also known as Kirksite or Zinc Alloy 2, Zamak 2 has the highest strength and hardness of the Zamak group of alloys.
ZAMAK 3 (ASTM AG40A)
Zamak 3, or Zinc Alloy 3, is the most commonly used zinc alloy in North America and has superb castability and excellent finishing characteristics.
ZAMAK 5 (ASTM AC41A)
Zamak 5, or Zinc Alloy 5, is the most commonly used alloy in Europe, has less ductility than Zamak 3, but also a higher copper content resulting in higher strength.
ZAMAK 7 (ASTM AG40B)
Zamak 7, or Zinc Alloy 7, is a variation of Zamak 3. It is a high-purity alloy containing lower magnesium content and has a tighter impurities specification. This results in enhanced casting fluidity, ductility, and surface finish.
ZA-8
ZA-8, or zinc aluminum alloy, contains significantly more aluminum than the Zamak group of alloys. ZA-8 contains approximately 8.4% aluminum and is the only ZA alloy that can be hot-chamber die cast.
ZA-12
ZA-12, or zinc aluminum alloy, contains even more aluminum than ZA-8. The number 12 represents the approximate percentage of aluminum.
ZA-27
ZA-27, or zinc aluminum alloy, contains even more aluminum than the ZA-12. It also has the highest strength, highest melting point, and lowest density of the ZA group.
MAGNESIUM DIE CASTING
The perfect combination of light weight, rigidity and resistance to wear for diverse die cast part applications.
ALUMINUM DIE CASTING
Creates very lightweight parts without sacrificing strength and offers a greater range of surface finishing options.
MAGNESIUM DIE CASTING
The perfect combination of light weight, rigidity and resistance to wear for diverse die cast part applications.
ALUMINUM DIE CASTING
Creates very lightweight parts without sacrificing strength and offers a greater range of surface finishing options.
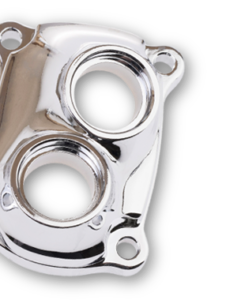
GET A QUOTE
Tell us about your upcoming project and our team will be in touch with you soon.
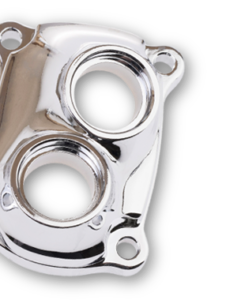
GET A QUOTE
Tell us about your upcoming project and our team will be in touch with you soon.