PACE INDUSTRIES
ALUMINUM ALLOYS
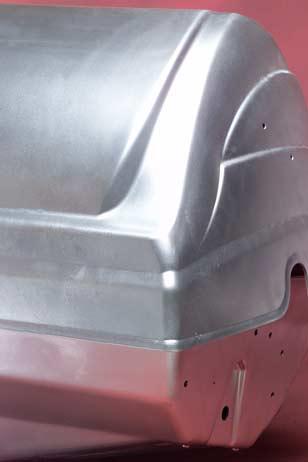
Aluminum die casting alloys (Table1) are lightweight, offer good corrosion resistance, ease of casting, good mechanical properties and dimensional stability.
Although a variety of aluminum alloys made from primary or recycled metal can be die cast, most designers select standard alloys listed below:
360 — Selected for best corrosion resistance. Special alloys for special applications are available, but their use usually entails significant cost premiums.
380 — An alloy which provides the best combination of utility and cost.
383 & 384 — These alloys are a modification of 380. Both provide better die filling, but with a moderate sacrifice in mechanical properties, such as toughness.
390 — Selected for special applications where high strength, fluidity and wear-resistance/bearing properties are required.
413 (A13) — Used for maximum pressure tightness and fluidity.
TABLE 1
COMPOSITION AND PROPERTIES OF ALUMINUM DIE CASTING ALLOYS
10.3
DESIGNATIONS AA NUMBER FORMER NO. COMPOSITION (in percent max. unless shown as range) |
A360.0 A360.0 |
A380.0 A380.0 |
E380.0 – |
383.0 – |
B383.0 – |
A413.0 A13 |
B390.0 390 |
384.0 384 |
Silicon |
9.0-10.0 |
7.5-9.5 |
7.5-9.5 |
9.5-11.5 |
9.5-11.5 |
11.0-13.0 |
16.0-18.0 |
10.5-12.0 |
Iron |
1.3 |
1.3 |
1.3 |
1.3 |
1.3 |
1.3 |
1.3 |
1.3 |
Copper |
0.6 |
3.0-4.0 |
3.0-4.0 |
2.0-3.0 |
2.0-3.0 |
1.0 |
4.0-5.0 |
3.0-4.5 |
Manganese |
0.35 |
0.50 |
0.50 |
0.50 |
0.50 |
0.35 |
0.50 |
0.50 |
Magnesium |
0.40-0.6 |
0.10 |
0.30 |
0.10 |
0.30 |
0.10 |
0.45-0.65 |
0.10 |
Nickel |
0.50 |
0.50 |
0.50 |
0.30 |
0.30 |
0.50 |
0.10 |
0.50 |
Zinc |
0.50 |
3.0 |
3.0 |
3.0 |
3.0 |
0.50 |
1.5 |
3.0 |
Tin |
0.15 |
0.35 |
0.35 |
0.15 |
0.15 |
0.15 |
0.20 |
0.35 |
Titanium |
– |
– |
– |
– |
– |
– |
0.20 |
– |
Total others |
0.25 |
0.50 |
0.50 |
0.50 |
0.50 |
0.25 |
0.20 (0.10 ea.) |
0.50 |
Aluminum |
Bal. |
Bal. |
Bal. |
Bal. |
Bal. |
Bal. |
Bal. |
Bal. |
PROPERTIES (see notes) | ||||||||
Ultimate tensile strength (ksi) |
46 |
47 |
47 |
45 |
45 |
42 |
40.5 |
48 |
Tensile yield strength (ksi) |
24 |
23 |
23 |
22 |
22 |
19 |
35 |
24 |
Elongation (% in 2″ G.L.) |
3.5 |
3.5 |
3.5 |
3.5 |
3.5 |
3.5 |
1.0 2.5 |
|
Hardness (HB) |
75 |
80 |
80 |
80 |
80 |
120 |
85 |
|
Shear Strength (ksi) |
26 |
27 |
27 |
25 |
25 |
29 |
||
Charpy impact strength (ft. lb.óunnotched) |
4.2 |
3.5 |
3.5 |
2.0 |
||||
Fatigue strength (ksi) (limit @ 500 million cycles) |
18 |
20 |
20 |
19 |
19 |
20 |
20 |
|
Density (lb./in.3) |
0.95 |
0.98 |
0.98 |
0.97 |
0.97 |
0.96 |
0.99 |
0.98 |
Melting range (oF) approx. |
1035-1105 |
1000-1100 |
1000-1100 |
960-1080 |
960-1080 |
1065-1080 |
945-1200 |
960-1080 |
Specific heat (Btu/lb.oF) |
0.23 0.23 |
0.23 |
0.23 |
|||||
Coefficient of thermal expansion (in./in./oF) |
11.8 |
11.7 |
11.7 |
11.5 |
11.5 |
10.3 |
11.7 |
11.3 |
Thermal conductivity (Btu/fthr.oF) |
65.3 |
55.6 |
55.6 |
55.6 |
55.6 |
67.7 |
78.6 |
56 |
Electrical conductivity (% IACS) |
29 |
31 |
31 |
23 |
23 |
31 |
25 |
23 |
Modulus of elasticity (106 psi) |
10.3 |
10.3 |
10.3 |
10.3 |
10.3 |
10.3 |
11.9 |
10.3 |
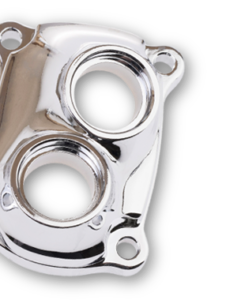
GET A QUOTE
Tell us about your upcoming project and our team will be in touch with you soon.