PACE INDUSTRIES
MAGNESIUM ALLOYS

Magnesium alloys are noted for low weight, high strength to weight ratio, exceptional damping capacity and ease of machining. Magnesium die casting temperatures are about the same as aluminum and both hot chamber and cold chamber die casting machines are used to produce castings.
Magnesium die casting rates are high because of its low heat content which produces rapid solidification. For the same reason, less energy is required to heat the metal to casting temperature.
AZ91HP (high purity) alloy has been developed for die casting parts subject to corrosive environments. Because of lower levels of nickel, iron, copper and silicon versus AZ91D, this alloy is finding applications in automobiles, computers and peripheral equipment and in other die casting products where paint or coatings are either undesirable or expensive.
Although magnesium die castings are used uncoated, they can be finished in a variety of ways to give increased protection against corrosion, wear and abrasion resistance and to improve appearance. Common inorganic treatments include chemical dips, anodizing and plating. Organic coatings — oil, wax, resin or paint — are usually applied over chemical treatments or anodizing to seal the surface.
TABLE 3
COMPOSITION AND PROPERTIES OF MAGNESIUM DIE CASTING ALLOYS
DESIGNATION ASTM COMPOSITION percent unless shown as range |
STANDARD ALLOY AZ91D |
HIGH PURITY ALLOY AZ91HP |
AM60B |
Aluminum |
8.3 to 9.7 |
85. to 9.5 |
5.5 to 6.5 |
Zinc |
0.35 to 1.0 |
0.45 to 0.9 |
0.22 max |
Manganese, min. |
0.13 |
0.15 |
0.24-0.6 |
Silicon, max |
0.5 |
0.20 |
0.10 max |
Copper, max |
0.30 |
0.015 |
0.010 max |
Iron 0 |
0.005 |
0.005 |
|
Nickel, max |
0.03 |
0.001 |
0.002 max |
Others, total, max. |
0.3 |
0.01 |
0.02 |
Magnesium |
Bal. |
Bal. |
Bal. |
PROPERTIES AND CONSTANTS | |||
Tensile Strength, (ksi) |
34 |
34 |
32 |
Tensile Yield Strength (0.2% offset) (ksi) |
23 |
23 |
19 |
Elongation, (% in 2″ G.L.) |
3 |
3 |
8-Jun |
Shear Strength, (ksi) |
20 |
20 |
N/A |
Compressive Yield Strength, (ksi) |
22 |
22 |
19 |
Ultimate Compressive Strength, (ksi) |
58 |
58 |
– |
Fatigue Strength, (ksi) (limit @ 500 million cycles) |
14 |
14 |
– |
Specific Gravity |
1.80 |
1.80 |
– |
Density (lb./in.3) |
0.066 |
0.066 |
0.065 |
Melting range |
875-1105oF |
875-1105oF |
1005-1140oF |
Thermal conductivity, CGS |
0.17 |
0.17 |
– |
Thermal Expansion, in./in./oF (x10-6) |
15.2 |
15.2 |
14.2 |
Electrical Conductivity, (% I.A.C.S.) |
10 |
10 |
– |
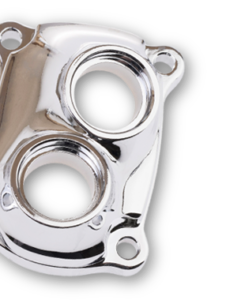
GET A QUOTE
Tell us about your upcoming project and our team will be in touch with you soon.